Genchi Genbutsu, Gemba Walks: Problem-Solving For Managers
- Alexandre Chatelier
- Oct 20, 2022
- 4 min read

What does Genchi Genbutsu mean?
Translated literally from Japanese to English, Genchi Genbutsu means "real location, real thing". The Genchi Genbutsu principle is also referred to as "go and see".
It's one of the 13 pillars of the Toyota Production System or "Toyota Way", and an essential principle within the organisation from a problem-solving perspective. Genchi Genbutsu also constitutes an essential element of lean management.
While the term Genchi Genbutsu represents an overall principle, the "Gemba" walk is the way the principle can be exercised and applied by managers. Gemba walks consist in - when a workplace problem arises - going on-site to observe what is happening and better understand the situation.
Can Genchi Genbutsu be applied in all workplaces?
Originally, the concept of Genchi Genbutsu was to be applied to production locations. Managers were encouraged to be on-site in order to fully understand the manufacturing process: what was going well, what needed to be improved, and the problems that needed to be solved.
Let us dive into the value of Genchi Genbutsu, Gemba walks, and how these can be of value to the "modern manager", and the value they can bring to other types of workplaces.
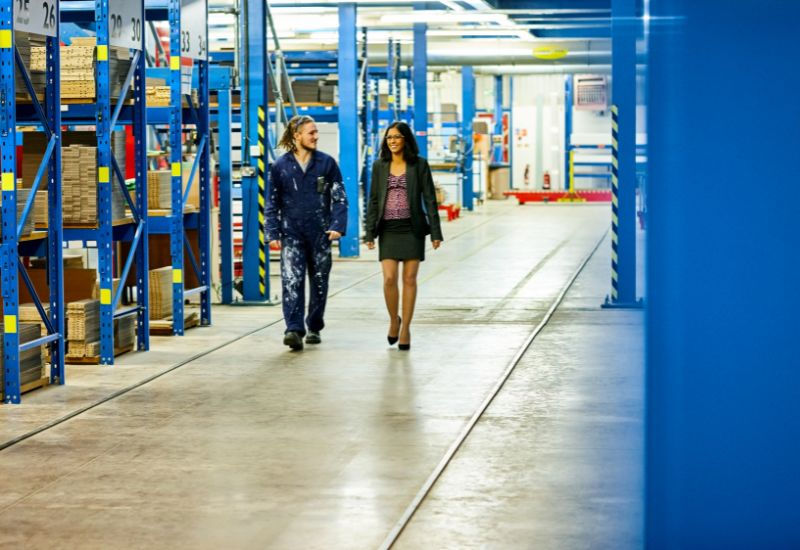
What is the Gemba Walk?
In practice, the Genchi Genbutsu principle can be applied through what are called "Gemba walks". The purpose of Gemba walks is for managers to deliberately witness the situation at hand, and understand realities by directly observing what is occurring on-site.
While the primary function of Gemba walks was to be applied to manufacturing and production sites, we found it interesting how it could be applied to other forms of workplaces, units, and organisations.
Gemba walks are often confused with Management by Walking Around (MBWA), brought to light by the Hewlett Packard Corporation in the 70s. The main difference between Gemba walks and MBWA is that Gemba walks have a specific purpose: gathering information to solve specific problems at hand and create a strategy to solve that issue.
How Gemba walks can have a positive impact on the workplace
1. Solving problems faster
Project management tools, emails, instant messaging, data, and many other collaboration channels can be very efficient to communicate problems organization-wide.
However, managers going directly on-site to gather first-hand information with the objective to solve problems may have a better understanding of projects employees are currently working on, and thus understand problems better if or when they arise.
How Genchi Genbutsu may help managers solve problems faster
Managers who take the time to be on-site and interact with their team will always have a head start in terms of understanding workplace-related problems, whether they involve employees, clients, or other issues that typically arise in organisations.

2. Diminishing hierarchy
In many workplaces, superiors and subordinates are not in the same room, not even on the same floor. This is not a problem in itself and if you're in a large company, the odds are you might need an entire building to operate.
However, being physically distant, superiors and employees may find it more difficult to communicate, collaborate, and find moments for small talk, all essential for a long-term work relationship.
In addition, for some employees, having a boss in the "corner" office or on the "top floor" may give a feeling of inaccessibility and a large difference in terms of status. In practice, having a certain hierarchy is arguably better for organisations to operate more efficiently.
How Genchi Genbutsu may diminish hierarchy
By being on-site when a workplace issue arises, managers can convey a stronger feeling of accessibility to their employees.
For some employees, knowing a manager is present, on-site, and "going and seeing" is comforting and perceived as a manager who cares about how their working day is going, if they are facing any bottlenecks, and how they can be helped.
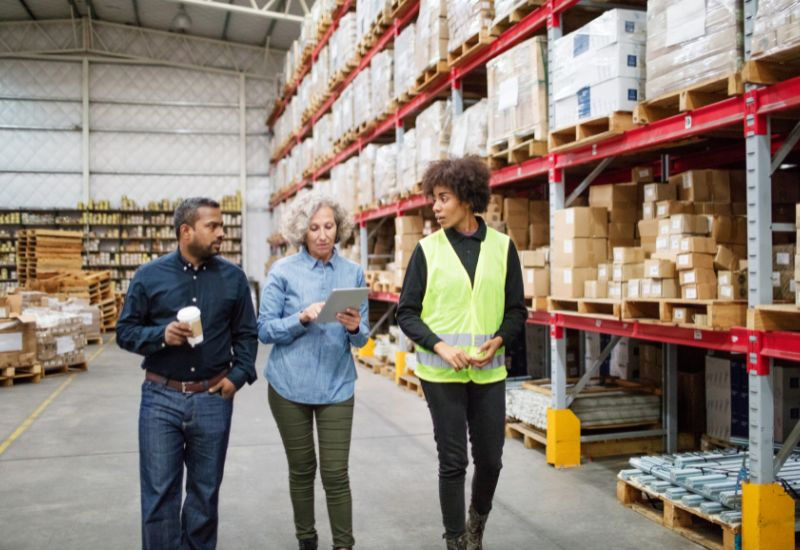
3. Building a solidarity-based company culture
In turn, managers taking the time to "walk the shop floor" when a workplace issue comes up demonstrate capacities of openness, interest, and empathy towards employees. These are features workers look for in almost every leader they want to work for.
By walking around the "actual place" and witnessing the "actual thing" happening in the workplace, bosses also indirectly communicate solidarity towards their employees. I mean, unless you haven't done your work well or you really don't like your boss: isn't it a good feeling to have him or her there?
How Genchi Genbutsu may help managers build a solidarity-based culture
I stumbled upon a LinkedIn comment from an employee who described how his boss applied the Genchi Genbutsu concept (whether it was consciously or not). This worker's division boss had a daily 2-hour slot in his agenda titled "Walk the floors".
This worker had "never seen a leader having such a grasp on every element of the business he managed". Another LinkedIn user said her manager spent his lunch break walking from table to table with his tray, establishing rapport with employees and displaying openness.
Final thoughts
In sum, Genchi Genbutsu, a key Toyota principle which means "go and see" - and Gemba walks - the act of going and seeing - may be interesting problem-solving approaches managers can consider when solving workplace-related problems.
Not only is first-hand information more accurate than reports or emails, the mere presence of managers in situations where employees require support is a solid way to demonstrate leadership for team leaders.
Kommentare